
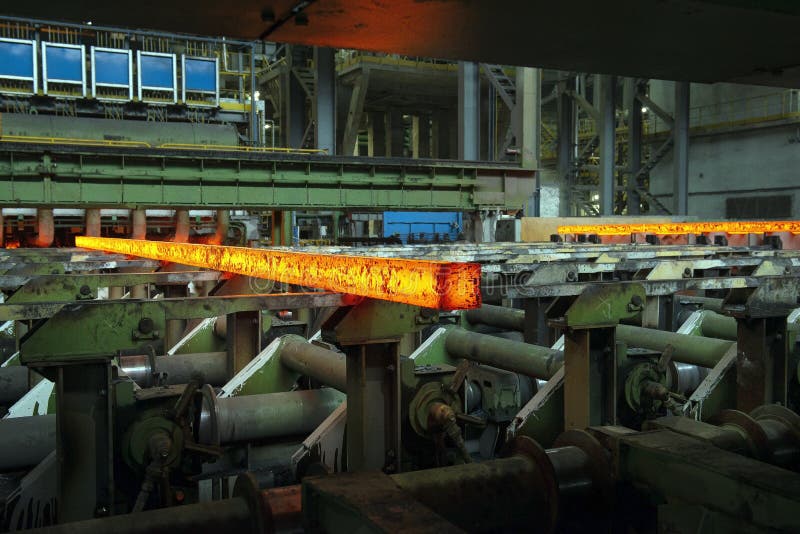

ISSUES TO OVERCOMEīesides nuclear power, most energy today comes from one of three hydrocarbon sources: petroleum, coal, and natural gas. Still, this idea may be closer than many realize as the idea of the Hydrogen Economy gains traction and support. A major obstacle to implementing hydrogen direct reduction ironmaking is the difficulty of producing enough hydrogen at a low enough cost without a large CO2 footprint, as it is done currently in steam-methane reformers. This concept, known as MIDREX H2, holds great promise in either new or existing MIDREX Plants. The ultimate method for drastically reducing the steel industry’s CO2 footprint is the use of green hydrogen (produced from renewable energy) for DRI production in a MIDREX Shaft Furnace. Yet, there is even more room for lower emissions through use of hydrogen as a fuel and chemical reactant in the MIDREX Process. By adding a CO2 removal system, the MIDREX Process can lower CO2 emissions even further to around 1/3 of the emissions from the BF/BOF route. The MIDREX NG™ Process paired with an EAF has the lowest CO2 emissions of any commercially proven steelmaking route using virgin iron ore at 1.1 – 1.2 kg CO2/kg steel. As a result, BF/BOF emissions can be 1.6-2.0 kg CO2/kg steel depending on the technologies used. The BF uses coke (refined coal) as the energy source and as the reductant to make iron with ~4.5% carbon, which is burned in the BOF to produce energy. The steel industry, especially traditional ironmaking, is among the largest contributors of greenhouse gases emissions – in the range of 7-9% of total emissions – because of its significant reliance on coal.Ībout 75% of the world’s iron is made using blast furnaces (BF), which is refined in a basic oxygen furnace (BOF). CO2 reduction from the industrial sector is widely recognized as a key to achieving these targets. The goal of this agreement is to increase the global response to the “threat of climate change by keeping a global temperature rise this century well below 2 degrees Celsius above pre-industrial levels”. The Paris Agreement opened for signature on Earth Day 2016 and entered into force on 4 November 2016. The only emission from using hydrogen as fuel or in fuel cells is water. Proponents of a world-scale Hydrogen Economy argue that hydrogen can be an environmentally cleaner source of energy to end-users without the release of pollutants, such as particulate matter or carbon dioxide at the point of end use. It has been put forth to solve some of the negative effects of using hydrocarbon fuels, which release carbon to the atmosphere as CO2, CO, unburnt hydrocarbons, etc. The Hydrogen Economy is a proposed system of delivering energy using hydrogen. As green hydrogen becomes available and cost effective, the MIDREX Process can be converted to MIDREX H2 in stages allowing steelmakers to take advantage of CO2 reduction immediately and further reduce emissions in the future without major capital expenditure. This article discusses the status of the transition from a Carbon Economy to a Hydrogen Economy, its challenges, and various ongoing activities. Unfortunately, hydrogen is not currently available at sufficient scale and low enough cost for rapid adoption. The best possibility for significantly reducing the CO2 footprint now and in the future is to use green hydrogen to produce DRI/HBI, which then can be used as feed-stock for steelmaking. While the MIDREX® Process using natural gas, paired with an electric arc furnace (EAF) has the lowest CO2 emissions of any steelmaking route using iron ore, there is room to further decrease emissions using hydrogen as a fuel and chemical reactant in the direct reduction process. Mitigating carbon dioxide (CO2) emissions in the iron and steel industry will become even more critical in Western Europe as the cost of CO2 emissions increases over time.
